FUTURE DRIVES ON INTELLIGENCE
Time: Sep 22th 2017 Copy editor: Tyrefull
The inevitable is happening. The world’s auto capital is shifting to Silicon Valley from Detroit! It is a euphemism to the transformation that is happening in transportation technology. Artificial intelligence and robotics have begun to drive the auto innovation frenzy. Enterprises are becoming lean and shedding weight in order to add muscles of efficiency and cost competitiveness. Vehicle light-weighting is impacting tyre designs and materials. Embedded electronic chips are being used to build intelligent tyres for vehicles that run on autopilot. Elon Musk’s Tesla is taking the current lead in autonomous cars while in the case of the tyre industry the charge is being led by Bridgestone, Michelin, Continental, Goodyear, Pirelli, and Yokohama Rubber. They are making disruption in tyre design and manufacturing. However, tyre and auto makers are cautiously worrying about additive manufacturing or 3D printing, which is set to see a revolution in vehicle and tyre production. Sharper customization allows individual buyers to choose the car and tyre of their choice from a portfolio of designs held in electronic files for 3D printing of the products. These developments are progressing at a clip that reminds of sci-fiction scenarios that are zooming into reality.
Tyres are shedding weights and are taking new shapes. The incredible changes are in line with the explosive transformation in technologies in the automobile industry. To cater to the proliferation of electric vehicles, OEMs are scrambling for new materials and electronics to produce intelligent tyres. They are intended to be capable of delivering exceptional properties demanded by emerging complex mobility demands.
The automobile industry itself is cruising down the highway of unprecedented changes. Under government emission regulations, vehicle makers are under pressure to switch from pollution spewing internal combustion engines (ICEs) to electric drivelines. This switch demands lighter tyres with the lowest possible rolling resistance.
The only reason that may be considered a drag on the potentially huge demand growth of EVs is the cost-competitiveness that ICEs still enjoy. Although the spark of the engine is dimming, production lines have not dried up. But people are more aware of the environment damage being wrought by the oil guzzling transportation sector. It contributes to almost 14 per cent of global greenhouse gas (GHG) emissions and results in the death of six million people annually.
After two decades of bitter wrangling, 200 countries have accepted the Paris climate deal that marked the beginning of a challenging journey to end the fossil fuel era and achieve a net zero emissions in the second half of the century.
In Asia, it is China that showed others the lead to follow the EV route. EVs constituted only 1.5 per cent of its national fleet, but more than 40 per cent of the EVs sold in the world last year were in China. It is twice as many as were sold in the US. Recently, India has announced plans to ban the sale of new diesel and petrol cars from 2030 and hopes to see six million EVs on roads by 2020.
Chinese-owned Volvo, the world’s first traditional carmaker to announce total phasing out of ICE vehicles, has said it would launch five types of EVs between 2019 and 2021 to take global lead in the electric race with one million units by 2025. In tandem with EVs demand growth, tyre makers have no choice but to re-jig their production and manufacturing strategy on the product front.
EVS TO SHOW THE WAY
As most EVs are designed to extract more mileage out of each watt, light-weighting is an engineering challenge for them. Tyres also need to be lightweighted and should deliver the lowest rolling resistance. Tyre engineers have to ensure that their products do not suffer ride quality, offer ease of handling and safety and assure durability while providing wet-road grip.
The challenge before them is to address these contradictory demands and discover materials that can produce ‘greener’ tyres that also offer lower weight. What they are constantly doing is to overcome rolling resistance and use new forms of silica and nanomaterials. It is the ‘magic triangle’ that is their perennial problem. Those companies that achieve breakthrough in these fields would be market leaders.
Embedding sensor chips in tyres is yet another challenge facing tyre engineers. The thrust is to make ‘intelligent’ tyres, which market analysts say are going to be the most critical factor for customer satisfaction in the coming years. This segment is to set to record 290 per cent compound annual growth rate (CAGR) in the next four years.
This will be on the back of connected cars that will be equipped with internet and wireless services that are aimed to ease driving by providing navigation, tyre pressure monitoring, tracking of stolen vehicles, quick ways to seek roadside assistance and make automated emergency calls. This will become more acceptable when battery-less sensors become cheaper.
Although intelligent tyres would lure more customers to buy them, there is also a rising demand from fleet operators who want them fitted on their commercial vehicles. Fleet managers expect that by constantly monitoring tyre pressure they could hope to reduce consumption of fuel, extend tyre life, achieve fewer number of vehicle breakdowns and ease vehicle tracking. The demand for such ‘smart tyres’ or ‘cyber tyres’ is expected to further rise dramatically.
Intelligent tyres are designed to monitor tyre pressure and transmit it along with temperature, average load, tread depth and precise readings of road conditions to optimise control of the vehicle’s dynamics. Dramatic breakthroughs in traction technology will lead to a quantum leap forward in vehicle driving dynamics. Vehicles will be rolling on intelligence tyres that can ease driving on any kind of road surface.
ADVANCED MATERIALS
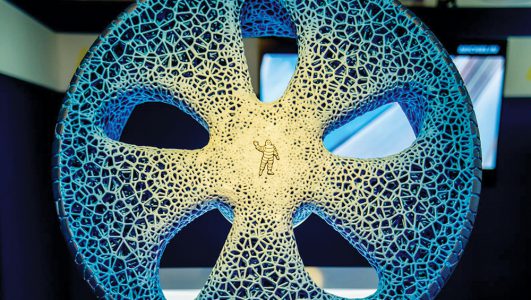
Michelin’s 3D printed Vision
Says Dr Aurp Kumar Chandra (see side story), a distinguished rubber and tyre technologist who was the Head of Global R&D at Apollo Tyres for more than a decade and is currently its Head of Special projects: “Tyre researchers are continually working on advanced tyre materials and tyre construction.” He expects dwindling use of NR and greater use of other naturally occurring rubber like guayule and Russian dandelion, synthetic rubbers like polyisoprene, butadiene rubber (BR) and styrene butadiene rubber (SBR).
Presently about 70 per cent of world consumption of natural rubber goes to tyre production. It is the price that mostly influences tyre makers to decide whether to use natural rubber or synthetic rubber and their combinations. The percentage of NR or SR in tyre is about 35 per cent each in tread and carcass, 15 per cent for sidewall and the remaining 15 per cent in the liner.
Dr Chandra notes that solution SBR, which is widely replacing emulsion SBR in passenger radial tyres, offers lower rolling resistance and better wet grip, which is ideal for EVs. Conventional SBR grades will get replaced slowly and he sees disruptions in elastomers developments to meet the challenges ahead.
Well-known futurologist Matthew Griffin (see separate story), who is described as the ‘adviser behind advisers’, forecasts in an interview his projections of major developments in the tyre industry in the next one or two decades. “I think there will be several but whether they materialise will depend on the incumbents’ appetite to reinvent the wheel,” he says. There are two areas that are ripe for re-development and innovation. The first is in the materials themselves, especially in nanotechnology, he points out.
He also expects tyre makers to closely collaborate with car manufacturers to create electro drive wheel systems that aren’t connected to the car, instead they’re held in place, spin, and are controlled by electromagnets. And the fact they don’t have any moving parts will make these systems more reliable and less costly to manufacture and maintain.
However, the use of elastomers will continue for a long time amid rapid advances in tyre materials. The demand will be dominated by sustainable materials instead of fossil fuel derived materials. Already renewables such as vegetable oils are being tried as substitutes for petroleum products in elastomer compounds. Future bio-based tyres will see stepped up efforts at reducing carbon footprints. Developments in guayule and Russian dandelion biopolymers point to that direction in material use.
INDUSTRIAL REVOLUTION
What is happening now is that tyre manufacturers are increasingly embracing the fourth industrial revolution or ‘Industry 4.0’ that will see greater automation in production with the widespread use of intelligent robots to produce cost-competitive tyres. The digital transformation in production is the way the tyre industry can hope to remain in the reckoning and produce innovative tyres that EVs of tomorrow require, says Alasdair Gilchrist (see separate story), author of Industry 4.0.
Automation in such diverse areas of value creation will lead to enhanced efficiency in the production processes. It will unlock the power of manufacturing. Industry 4.0 can optimise their operations and increase profitability by automation and supply chain efficiency. After all profits equals revenue minus operational cost. “Therefore, I think we will see at the top end of the Asian tyre market strenuous moves to adopt Industry 4.0,” says Gilchrist.
There are fears of massive layoffs of workers following automation in a hyper-connected world. It is reckoned that two billion jobs or 50 per cent of the jobs globally will disappear by 2030. This anxiety is reflected in the tyre industry also in the light of anticipated disruptions in future mobility revolution. Its cornerstones are zero emission, zero accidents and zero ownership.
The connected vehicles with electronic sensors on board and moving on intelligent tyres are susceptible to cyber attacks. Hackers can potentially undermine the complex algorithms run on distributed computer platforms that guide sensor-based vehicles and tyres. Imagine this in the context of prediction that there will be 200 billion connected devices by 2020.
The future of the tyre, the emerging scenarios of autonomous vehicles plying on our roads and Industry 4.0 manufacturing capabilities would take humanity to the next exciting level of mobility since the development of the automobile and tyre over a century ago. The disruption in this field received further impetus with 3D printing, also known as additive manufacturing. It is set to shape the future development in industrial manufacturing with printed tyres and auto parts.
Already over 70 per cent of US manufacturers are using 3D printing technology to make prototypes to the final products. Software coders are frenetically writing programs as the market for 3D printing is galloping. While developers will be worried about their exposure to intellectual property issues, consumers will be insisting on micro choices for their vehicles and tyres that could be rolled out through 3D printing.
DEMOCRATISING MOBILITY
Analysts say micro automakers – similar to microbreweries – are emerging. They will lead to ‘democratisation of the auto industry’ through 3D-printing technologies. They are expected to make tyres and vehicles more affordable. The era of built-to-taste vehicles such as the world’s first 3D-printed supercar Blade, has marked a revolution in car manufacturing that will be environment friendly and sustainable. Such innovation is also triggering attempts at 3D printing of tyres on mass scale.
As additive manufacturing picks up pace, tyre makers will boost disruption with new materials. The future trend could see manufacture of customised cars in low volume, and at the same time cheaply. Ford is testing large-scale 3-D printing technology for car parts that it expects to be a breakthrough for vehicle manufacturing. The advantage is that it could test cheaply the car’s efficiency and deliver at lower costs. There is a sunny outlook for 3D printing in the auto industry, says Richard Hanna, global leader of automotive at PricewaterhoseCoopers.
Michelin unveiled the tyre of the future in July. It was a 3D-printed tyre-wheel combination that could be altered and customised based on driving needs. Called the Vision, the ‘smart tyre’ can give drivers detailed information about its condition. It would not face blowouts, explosions, or flats.
As he unveiled the tyre, Michelin’s Executive Vice President of R&D Terry Gettys said: “This airless structure would allow us to replace tyre and wheel combinations of today. We’ve profited from our research on airless tyres to understand how to distribute the load carrying capability so that you have enough rigidity to carry the load, enough to steer the vehicle, and maintain stability, and yet not too much rigidity in order to maintain comfort.”
What makes the Vision unique is its ability to be altered and customise the tyres for different journey. “You would drive your car up to a service centre and there would be four 3D imprinting modules that come and they clean your tyre to prepare it and depose new material in the form of the new design onto the same structure that you already had on the vehicle, but customised for your actual journey.”
Although taking Vision to market will take time – it won’t be available for 15 to 20 years – the race for customised tyres of the future is in the fast lane.
AD: You can get better price from us for Doublestar tire. Doublestar brand tire is the TOP 10 Chinese brand tires since 2004. Give us a call and you would get a surprice price!